国内自動車メーカーがアルミニウム合金で大型部品を一体鋳造する「ギガキャスト」の導入を本格化する。ホンダは、米国のアンナ工場(オハイオ州)に新設する電気自動車(EV)用電池ケースの製造にギガキャストを用い、車体骨格部品への展開も検討する。トヨタ自動車も2026年に市場投入するEVの車体にギガキャストを用い、日産自動車も27年度から採用する方針だ。各社はギガキャストでEVの製造コストを一気に下げたい考えだが、実用に向けた課題も残る。
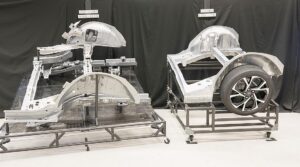
ギガキャストは、溶接やボルトで接合していた車体部品を、巨大アルミな鋳造設備で一体成形するダイカスト技術の一種だ。部品点数と工程の削減、製造サイクルタイムの短縮に加え、軽量化も図れる。溶けたアルミを高速で射出する点で、重力により溶けたアルミを型に流し込む「金型鋳造」などと区別される。
アルミ鋳造自体はエンジンブロックや変速機ケースですでに用いられているが、型締め力は3千㌧級が一般的だ。ギガキャストは型締め力で5千㌧級以上を指すことが多い。EV専業のテスラが「モデルY」のフロントとリアのアンダーボディーで用い、注目を集めた。
ホンダは、EVに搭載する電池を薄くするため、電池ケースにギガキャストを採用する。アンナ工場に大型ダイカストマシンを含む生産ラインを新設する。アルミ同士やアルミと異なる材料を接合するFSW(摩擦撹拌接合)技術とギガキャストの採用で、電池ケースに用いる部品の点数を60部品から5部品に集約できるという。
実用化に向け、栃木にある生産技術の研究拠点に型締め力が6千㌧級の大型ダイカストマシンを導入し、量産技術を確立する。EVのボディー骨格部品にギガキャストを用いる研究開発も急ぐ。
トヨタも、26年に市場投入する次世代EVにギガキャストを採用する方針を明らかにしている。フロント、リアそれぞれのアンダーボディーにギガキャストを採用する技術を開発中だが、実用化するモデルのどの部分に採用するのかは未定だ。グループのアイシンも、ギガキャストによるフロント骨格や電池ケース製造に参入する。
日産も型締め力6千㌧級の大型ダイカストマシンを導入し、27年に市場投入するEVのリアアンダーボディーの一部にギガキャストを用いる。約100部品を1部品に集約でき、鋼材と比較して重量が3割軽くなるという。
ギガキャストはテスラのほか、ゼネラル・モーターズ(GM)、ヒョンデ、ボルボ・カーズや中国系EVメーカーがすでに実用化している。EVのコストを引き下げる技術として注目されている。
ただ、アルミ合金は鉄鋼に比べ割高なことに加え、鋼板と比べて伸びが小さく、衝突安全性の確保や接合などの製造品質に課題があるとされる。
アルミは修復が難しく、リペアビリティ(直しやすさ)を保つ工夫も必要だ。また、大型ダイカストマシンは巨大で、金型だけでも100㌧前後ある。特に日本国内で生産する量産車に導入するには輸送面などでハードルが高い。
日系各社は、低圧化技術や金型の最適化、短時間注湯など実用化に向けた開発を急いでいるが、狙いどおりEVの競争力強化につながるか注目される。
※日刊自動車新聞2024年(令和6年)5月22日号より